3 Ways to Transform Your Business Using a Low-Code App Builder
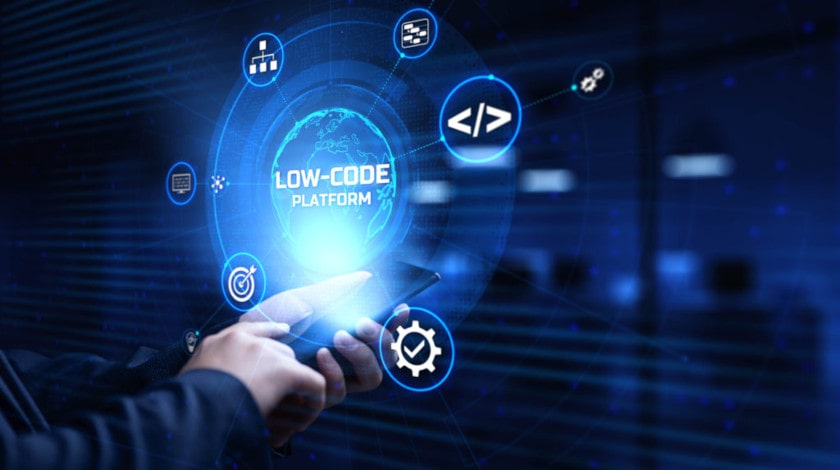
No-code and low-code app development is certainly a hot topic across a mix of industries and professions. Low-code app builders have become increasingly appealing to business leaders who either don’t have the bandwidth or the expertise to develop software to meet their operational needs. Businesses are able to save money by bringing on a new tool versus a team of developers to create an application that works for their business needs.
Low-Code and No-Code App Development Can Transform Your Business
To join in on the low-code/no-code buzz, we are highlighting three companies who have transformed their operations in different capacities with the help of Device Magic’s low-code app builder. Our hope is to provide you with a little inspiration as you investigate low-code tools and how they can help you achieve your business goals. So let’s get started!
1. Scale a New Business Line
Company Background:
Farmers National Company is the largest agricultural land management and real estate firm in the United States. The company manages 5,000 farms and sells about $450 million in farm property each year. In recent years, lending banks began contacting Farmers National to see if they could conduct comprehensive inspections of agricultural assets and properties to make sure they matched up with the information provided by loan applicants. Farmers National had the expertise, so they set up an internal division to begin offering collateral inspection services.
The Challenge:
It was quickly evident that Farmers National wouldn’t be able to scale the new collateral inspections business line with the highly manual, paper-based, time intensive process they had in place.
The Solution:
Senior vice president of sales and marketing, Matt Gunderson, and IT manager, Jim Manuel, onboarded Device Magic’s business app builder to transition from their paper-based process to a digital process. They used the app to configure the inspection forms, workflows and reporting exactly how they needed it before implementation.
The Result:
They went “live” with the tool and new process in the fourth quarter of 2020, and by the first quarter of 2021 they experienced significant return-on-investment. The app helped them reduce collateral inspection report processing time by 75 percent. Inspectors’ backend processing time was also reduced by nearly 50 percent. And best of all, the company was able to nationally scale the new collateral inspections business line. They increased the service line volume while maintaining the same overhead.
2. Streamline Your Production Process
Company Background:
FGP Manufacturing is a Mobile, Alabama-based company that specializes in premier ice pop contract manufacturing and co-packing. FGP is the sole supplier of all Frios Gourmet Pops, the leading popsicle franchise in the United States.
The Challenge:
As you can probably imagine, production demands began growing rapidly as Frios signed on more and more franchisees across the country. FGP needed a way to track critical data throughout all stages of their production process so they could provide full traceability and improve operational efficiencies. FGP’s production manager and head of food safety, Paul Costa, knew they couldn’t rely on manual paperwork to handle these demands.
The Solution:
Costa began researching low-code app builders because they needed a tool they could easily customize to fit their needs. He decided to onboard Device Magic, and began building an application that supported their unique production process. Keep in mind, Costa is not a developer. So the low-code aspect was crucial for him. He was able to figure it out fairly quickly, and leveraged the advanced form builder features, such as intelligent fields, conditional logic and backend calculations.
The Result:
Once FGP got the app ready for company-wide roll-out, it didn’t slow operations at all. They are now using the app throughout each stage of their production process. It serves as their digital recipe book. So when an employee is ready to create a new batch, they just open the mobile app and they’re able to see every ingredient, amount and lot code listed out in the form. Costa also created a batch conversion form so he can easily calculate the number of batches needed to hit their weekly targets.
At the shipping stage, FGP employees use the camera functionality to scan QR codes associated with each lot code for every single order. Now if there is a product recall, they can now process it in under 20 minutes by tracing lot codes back to the manufacturing date. The app has also provided new-found visibility to waste data.This has become a motivator for the whole team by allowing them to easily identify problem areas and make improvements.
3. Build an Industry-Leading Safety Culture
Company Background:
BriggsAmasco is one of the leading commercial roofing and waterproofing companies in the United Kingdom. The company was established in 1865, and has since grown to three different operating divisions performing everything from quick-turn repair jobs to multi-year, large commercial contracts. Throughout more than 155 years of operation, BriggsAmasco has always prioritized the health and safety of their employees. It’s actually one of the company’s core values.
The Challenge:
Safety quickly becomes complex at a large company like BriggsAmasco. The forms their safety teams have to fill out on-site have more than 33 sections that cover everything from toolbox talks to site contacts to inspection checklists. With the added logistics of managing these protocols across three separate operating divisions, maintaining optimal safety standards across the organization had become a cumbersome process.
The Solution:
BriggsAmasco’s IT manager, James Wood, needed to find an application that he could easily build to accommodate the company’s complex safety procedures and allow him to continue focusing on day-to-day IT support. During his Device Magic free trial, he discovered that it interfaced with their existing Microsoft Word forms through a simple mail merge and he could leverage live resources to input all 33 sections of the safety form into a single resource.
The Result:
Implementation of the app has helped ensure faster, more accurate safety data delivery and record keeping across the organization. With the live resource integration, Wood is able to implement form updates and changes within seconds.They have also been able to automate certain form components, such as input of the company division, logo, location, employee info and data retrieval workflows. As an example, SMS messages are automatically sent to appropriate parties when forms are completed.
Business App Building Made Simple with Low Code Solutions
Hopefully these case studies have given you some valuable food for thought. Whether you’re programming savvy or not, chances are your plate is already full. Enlisting the help of a low-code app builder can make your life easier as you work to achieve the digital transformation goals of your business. Take some time to research options and participate in free trials if the platform offers them. This way, you can find out which one is the right fit for your organization before making a commitment or investment.