How to Offset High Supply Prices & Material Costs
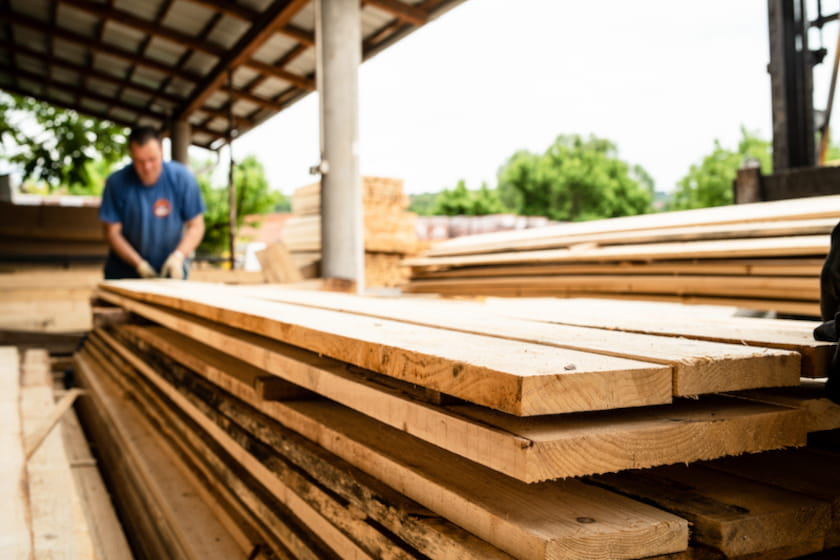
Among many other aspects of construction that COVID-19 impacted, the cost of supplies has been one of the most prevalent. Before the pandemic hit, supply costs were already increasing year after year – a fact that was even more evident each year during peak construction.
But the serious disruption to supply chains caused when COVID-19 demanded lockdown action across many industries and in many areas of the world has made supplies across the board harder to get, and the costs to get them almost unbearably high.
Take lumber: prices per thousand board feet were at $349 in April of 2020, but by May of 2021 the price was $1,514. Though prices for lumber have cooled in the past few months, they are still high, and those elevated prices are in addition to increases in the prices of copper, concrete, and steel.
How Long Will Elevated Prices Last?
Experts have indicated that the price increases resulting from COVID-created bottlenecks are probably temporary, and point to the drop in wood prices as an indicator of the beginning of the end. But the bottleneck is still backed up, with builders waiting on anything from doors to appliances. It seems it will take awhile before that backlog clears up and it’s unclear what will happen with prices by the time it does.
This is adding to owners’ bills during the building process, but contractors have been eating some of those costs as well. In order to keep costs low and work coming, it’s prudent to offset those increased costs in some other way.
Below are some of the best ways to keep your profit margins healthy in the face of increased supply costs.
Prefabricate
Prefabrication has been making waves in construction for awhile now – with technology that’s been rolling out over the past number of years it’s possible to build an entire building digitally, virtually walking through rooms and making changes as needed. Then, builders can order pieces to spec and fit them together on site.
Prefabrication brings a number of efficiencies to the construction picture that can offset rising costs. The majority of time is put into manufacturing, but takes fewer labor hours on the jobsite to construct prefab portions of a building. The manufacturing element lends bulk buying power to the process, and can lower the cost of supplies overall. Prefabrication can also lead to tighter and more certain schedules, so contractors can get more done in less time.
Finally, and possibly most pertinent to cost savings, is that there is less waste involved in prefabrication. Since all the pieces are cut to spec, builders order exactly the materials they need, no more, and each piece is used efficiently. Making better use of the raw materials can bring the price of building down.
Go Lean
Almost as hot a topic as prefabrication, lean construction offers many opportunities to cut costs along the way. Lean construction proposes early and frequent involvement of all parties involved in the construction process in order to make best use of each one’s expertise. This means, for example, getting subs involved in the design process to share their views on everything from jobsite layout to scheduling.
The idea behind lean is to break down silos traditionally separating one profession from another within the industry, and it can lead to some great results. By getting rid of waste from reworks, delays, overproduction, and inefficient use of people, research is consistently showing more projects being completed ahead of schedule and under budget when contractors embrace lean methodology. That is due, in part, to a 6-7% waste reduction and up to 9% improvement in productivity on these projects.
Think Nimble
The construction industry is nothing if not resourceful. This is the case with building supplies, too: sometimes a good stand-in can be the answer to supply chain disruptions. While some supplies may be must-haves for construction projects, others can be swapped for more affordable or more easily available alternatives..
If steel prices are at an all-time high, for instance, builders know they can turn to rubber-backed composite instead. While the latter is usually a premium cladding material, with steel prices higher than normal the two might be available at reduced material costs, and can be an affordable option to keep a project moving.
A TPO roof is an option in place of a metal roof, too, if owners are interested in trying something different. TPO is cheaper than a metal roof at the best of times, and the spread may only be widening.
Think quick and keep an open mind to suggest and implement changes to control supply costs during a build.
Use the Technology
A clear pattern is emerging here: contractors can achieve great cost control through efficiency of systems – sweating the details and making better use of resources can lead to huge results.
Technology continues to provide construction with tools to further improve efficiency. Whether it’s keeping better track of equipment, streamlining COVID reporting using QR codes, or making best use of people through workforce management tools, improving the construction process is made easier through digital tools.
The collaboration that is so crucial for improving systems is made easier when data can pass digitally through online forms to expedite approvals, track a project’s status, and improve safety tracking, among many other tasks.
Device Magic helps create custom forms to capture this type of data, and allows users to add photos and geotag their notes so all stakeholders are up to speed, whether or not they’re on site.
Changes to Systems Can Offset High Supply Prices
This efficient movement of information is key to collaboration, and helps bring people and ideas together to avoid waste.
Construction is a flexible and resilient industry. Controlling costs is possible using ingenuity and by continued learning of available tools and improved systems.