Construction’s New Normal: 3 Pandemic Shifts That Are Here to Stay
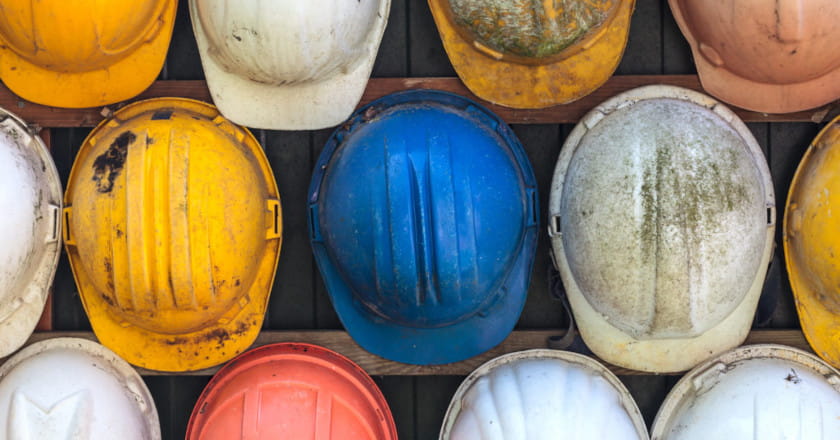
Businesses economy-wide had to make huge changes to their operations thanks to COVID-19. Construction, an industry that kept plugging away during much of the time that others were shut down entirely, was impacted from many different sides at once, and it’s one industry that may never go back to the way things were.
Across industries, companies figured out how to work at distances and make do with less, and the most flexible organizations were able to morph on the fly to meet new challenges. For its part, construction was impacted by:
- A continued worker shortage that began long before the pandemic
- Supply chain delays that also resulted in increased prices
- Limits to the amount of workers allowed on jobsites
- Tracking, social distancing, and appropriate PPE for workers that were on site
These challenges changed the way construction does business. Here are some of the long-term impacts of the pandemic that have created a ‘new normal’ for the construction industry, and the solutions emerging that will help the industry meet these challenges.
Increased Safety and Tracking
The continual improvement of safety protocols has been at the top of construction’s to-do list for just about ever, and that’s not about to change. What is changing are the metrics used to judge success, and the tools implemented to meet safety goals.
Top performers in construction safety these days rely on tracking near misses and documenting jobsites to monitor housekeeping progress and safety protocol implementation. Jobsite photo documentation tools that offer 24/7 views of the site and its upkeep are helping managers to conduct checks and walk-throughs regardless of their locations.
The virus is still very much a reality on jobsites, so continual contact tracing, daily worker health screenings, and worksite cleanliness are trends that will continue on jobsites through 2022 and beyond. Mobile digital forms like those created in Device Magic make it easier to accurately track the movement of people, and make it easier to share, store, and analyze information contained in them. Device Magic facilitates the creation of custom online forms that can collect more robust data sets that can include photos and geotagging.
Making Do With the Fewest Possible Workers Onsite
Construction has been dealing with a skilled worker shortage for some time, and retirements are further draining the talent pool – during the next decade, an estimated 41 percent of the current US construction workforce is expected to retire. Now that pandemic control efforts have lead to strict limits on site occupancy, and there are regulations that require tracking of all those who are present, the issue is all the more prescient.
Smarter scheduling management, in part through digital Gantt charts and workforce management tools, is enabling managers to better use the workers they have. With technological tools available now, managers can see around corners, better predicting when workers will be needed and when needed workers will be available, to schedule with more accuracy than ever before. New digital tools are also more easily altered than old paper methods, so when plans change managers can reconfigure schedules to find best possible outcomes.
Dealing With Supply Shortages, Delays, and Price Increases
Effective construction planning generally dictates that the ideal time for supply delivery is the closest possible time to when supplies will be needed, to avoid crowded worksites and damage to materials.
All that out goes out the window when supplies are hard to come by, or when the price of materials climbs so consistently that managers are driven to order before they’re priced out entirely. When lumber costs climbed from $349 per thousand board feet in April of 2020, to $1,514 in May of 2021, some contractors were stockpiling the stuff to avoid paying even higher prices down the line.
Lumber prices have since leveled out, but they’re still high, as are prices on supplies such as copper and steel. This is not likely going away – estimates are that prices on bricks, concrete, and cement won’t decrease anytime before summertime in 2022.
Planning and flexibility will be the keys to success for contractors in the face of these challenges. A 2020 McKinsey study indicates that companies will look to get into fabrication models of construction to control more of the construction process, and may even delve into supply ownership and manufacture. Schedules need to be laid out with built-in grace periods, and easily amended when things change.
Technological Tools Help Move the Industry Forward
Luckily, the technical revolution was ready for construction when the industry needed it most, and the resulting tech boom in construction has only just begun. The same McKinsey study says that, “Digital technologies can enable better collaboration, greater control of the value chain, and a shift toward more data-driven decision making,” all of which make it easier to do more with less – which is exactly what the industry is being asked to do.
Through these new tools and the resilience and steadfast nature it’s known for, construction will emerge stronger and more capable than ever.