Update Your Safety Inspection Report Process Step By Step
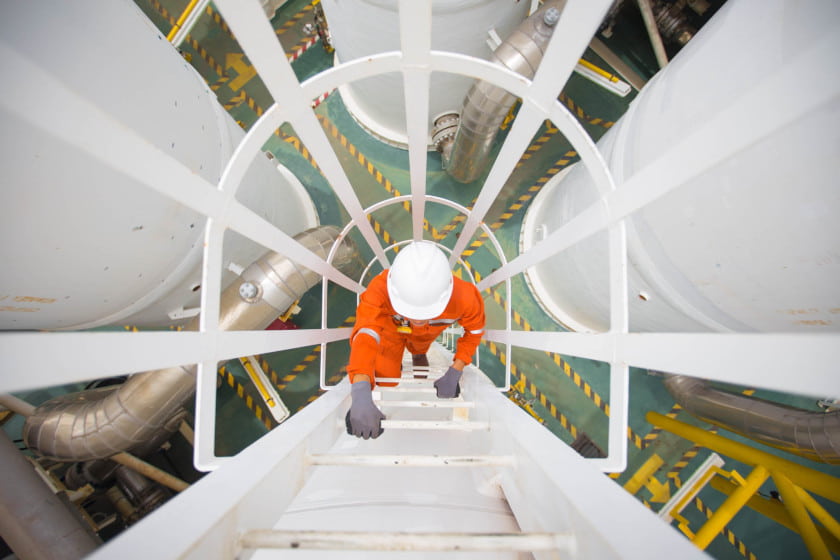
Using an out of date document is frustrating. A consultant recently shared an example from the financial industry. In this case, a policy document still listed Lehman Brothers even though the company has been out of business for nearly a decade. You don’t want that to happen with your safety inspection reports.
How Do Out of Date Safety Inspection Reports Hurt Your Company?
Out of date safety inspection reports do damage to your company. The harm is not always obvious, so let’s break it down.
- Disappointing new employees. When a new hire is asked to use out of date processes, it creates an unprofessional impression. Dated documentation and reports suggest the company is disorganized or can’t be bothered to stay current.
- Increased compliance risk. Governments make new rules every year. Further, many of these rules come with penalties. For example, OSHA applied over $250,000 in safety fines to Republic Steel in 2017. Preventative action may have been much cheaper.
- Decreased productivity. An out of date inspection report is harder for employees to use. Think about it. At each item, you have to ask “does this item still apply?” Those little delays add up to productivity losses.
Before going further, ask yourself which of the reasons above apply to your situation.
Reviewing Your Safety Inspection Process Step by Step
1. Why does the safety inspection report matter?
These documents are a key risk management procedure. They prevent injuries, deaths and damage. That’s why it matters to keep your safety inspection process current.
2. Are there company procedures you need to follow to update it?
Larger organizations are governed by policies and standards. If that is your environment, you need to follow these processes, especially when they relate to a safety matter.
Check your company’s internal website for standards. If there are no set policies governing safety changes, move on to the next step.
3. What is the company’s recent history of health and safety incidents?
A safety inspection report should not be a theoretical document. Instead, it should address the practical needs of your employees, contractors and other stakeholders.
For instance, injuries relating to construction tools may be a problem for your organization. In that circumstance, research ways to reduce that type of incident, and consider completing a job safety analysis to identify other hazards.
Tip: Go beyond formal reports. Some injuries and related incidents are not reported because they are minor. You can play a role in reducing those incidents by improving safety inspections.
4. What are health and safety trends are you seeing in the broader industry?
You can only learn so much by analyzing internal company data. Take some time to scan the broader environment for health and safety risks. You can use Google News to search for media reports of safety incidents. Further, take a look at reports issued by government agencies like OSHA.
Start by looking for incidents reported by your immediate competitors and then broaden your research to find additional examples.
Resource: If you are new to research, get in touch with your public library. Few companies take full advantage of all the research tools offered by their library. For example, you can find specialized publications like Safety+Health Magazine.
5. Identify leading indicators for safety incidents
Safety inspections are focused on nipping safety risks in the bud. In reviewing safety incidents, look for the “early warning signs” a safety inspection report can detect. For example, preventive maintenance and testing on elevators is a way of reducing the likelihood of a catastrophic failure.
On a construction site, a leading indicator could be fitting each employee with safety equipment. This leading indicator of safety approach will encourage your staff to use their safety inspection reports to stay safe.
6. Digitize the safety inspection report
Some industries like construction and the skilled trades still rely on paper forms to carry out much of their work. If your company relies on paper inspection reports, it is time to change.
After all, you are already investing time and effort to improve the design of your inspection report. Why not improve it further through digitization?
Instead of waiting until the end of the day, your staff can send a digital checklist immediately after finishing their inspection. That gives managers at the head office the opportunity to review the checklist quickly. If needed, you can ask staff to go back and inspect a certain safety aspect more deeply.
7. Test your new safety inspection report in the field
No improvement can be trusted until it is proven in the field. Ask a few of your inspectors to use the new form on a few different sites and share their feedback with you. If they provide vague feedback, tell them that the inspection report is still experimental and subject to feedback.
Tip: Struggling in your efforts to receive significant feedback from your field staff and customers? Take a look at the book “Crucial Conversations” — it has a proven process to navigate conversations with high emotions and conflict.