How Restaurant Equipment Services Group is Going Paperless
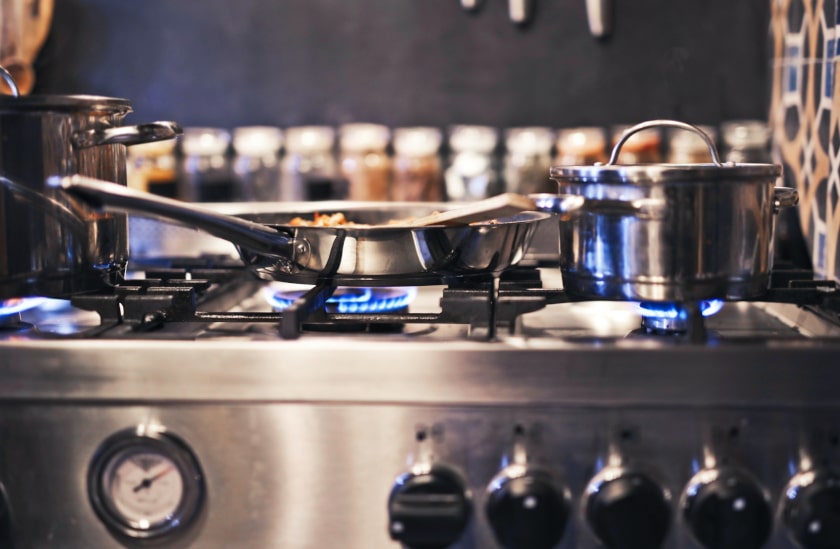
Safety and insurance compliance means paperwork. Lots of paperwork.
When Evan Davis joined Restaurant Equipment Service Group as IT & Asset Manager in the summer of 2013, he found himself surrounded by paperwork. Even with digital systems in place for their contracts and service orders, technicians were still completing mandatory safety reports for vehicles and equipment using paper forms. That lead to some time consuming processes, to say the least.
“I used to collect all these sheets and transcribe the data into an Excel spreadsheet,” said Davis. “It was a massive time suck. It would take me 2 hours a day just re-entering all the data.” He knew there had to be a better way. Then he found Device Magic.
A more efficient office with improved data quality.
Davis rolled out Device Magic on a trial basis to a single device. Three months later, Device Magic was being used on 40 Restaurant Equipment Service devices.
A large part of what Device Magic replaced was emails from the field to the office with vehicle and equipment inspection information. Techs were completing these inspections on paper and re-entering the information into an email that was sent to Davis. These emails lacked a consistent format and offered no quality control. There was no easy way to see if data was missing or inaccurate.
Using Device Magic’s drag-and-drop online form builder, Davis built two inspection forms in two hours for Restaurant Equipment Service Group techs and set up an email destination. Now, whenever an inspection form is completed, it is sent via a formatted email with all the questions answered. No more lost or incomplete questions. No more re-entering data.
Restaurant Equipment Service Group is now utilizing Device Magic on over 90 devices and has created over 35 different forms to utilize the many Device Magic features. They’ve expanded how they use Device Magic to include:
Part Requests – Used to ensure consistent information from field technicians every time.
Preventive Maintenance Checklists – To capture before and after photos and condition of equipment.
Quality Control and Job Site Safety Inspections – Completed after a technician has been on-site to ensure everything was initially covered.
Service Quotes – Used to ensure all items are covered when creating a quote for potential work.
Restaurant Equipment Service Group’s Story isn’t Uncommon
There are numerous industries where collecting data from the field is a major issue. Industries where re-entering data or relying on completed paperwork is the best option. Industries where the idea of going paperless and using cloud-based solutions or mobile technology is daunting. However, more and more companies like Restaurant Equipment Service Group are seeing the value in using technology and going paperless. Why? Because it makes businesses more efficient and saves them real dollars. And at the end of the day, what business doesn’t want that?