How Device Magic Became FGP Manufacturing's Digital Recipe Book
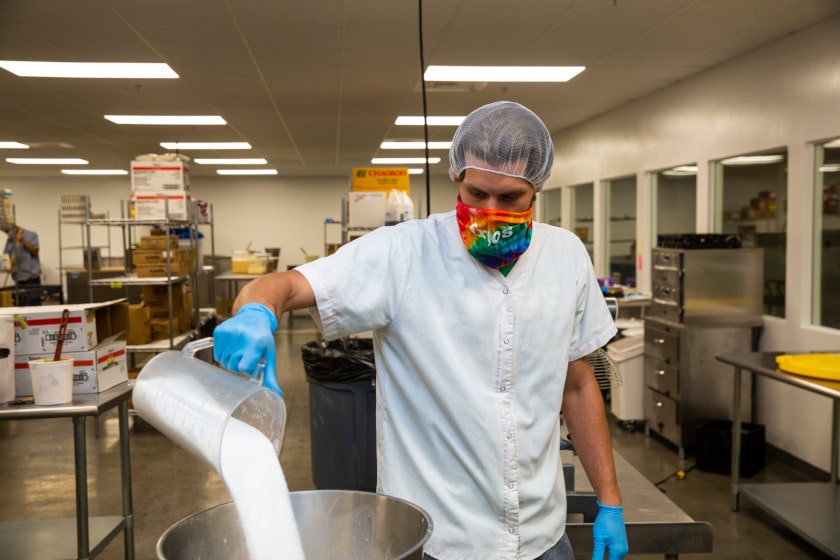
Popsicles may not be the first thing that comes to mind when you think of the food manufacturing industry. But somebody out there has to supply the everlasting demands for these frozen treats, right?
Let us introduce you to FGP Manufacturing. Headquartered in Mobile, Alabama, FGP specializes in premier ice pop contract manufacturing and co-packing. FGP is the sole supplier of all Frios Gourmet Pops, the leading popsicle franchise in the U.S. If you’ve ever tasted a Frios Pop, you already understand that FGP knows how to make a mouth-watering frozen dessert. However, as product demands continued to grow, FGP needed to find a way to scale their production process.
Finding the Right Fit for their Niche
FGP’s production manager and head of food safety, Paul Costa, began looking for a solution that could provide full traceability throughout all stages of the production operation, track critical data and improve efficiencies.
Manual paperwork was always out of the question for tech-savvy Costa. So he began researching several mobile data collection software options. He found Device Magic and was sold on the user-friendly interface and superior technical support.
“My big concern was finding a tool that my employees would use effectively and without a lot of resistance,” said Costa. “What I liked about Device Magic is that I was able to incorporate initial answers or hints. I was very meticulous about how the form fields were ordered and worded to make onboarding as seamless as possible.”
While Costa spent a considerable amount of time on the initial set-up and speaking with the Device Magic technical support team, it was all worth it. He finally found a tool that accommodated FGP’s unique needs. Once he got it to a comfortable point for roll-out, it didn’t slow operations one bit. It was a win for the whole team.
Mobile Forms: A Recipe for Success
Since implementing Device Magic, FGP has found many uses for the application. But perhaps the most important is the secret to their success: recipe perfection. Costa uses the live resource through Google sheets to reference every FGP popsicle formula.
FGP is using Device Magic throughout each stage of their three-step operation process. New-found visibility to waste data has become a motivator for the whole team by allowing them to easily identify problem areas and make improvements. At the shipping stage, FGP employees use the camera functionality to scan QR codes associated with each lot code for every single order. This alone has been a huge benefit when dealing with product recalls. Costa explained they can now process a recall in under 20 minutes by easily tracing lot codes back to the manufacturing date.
Device Magic was also an important tool in helping FGP achieve its BRC food safety certification. Costa built customized forms to cover all the certification requirements and pre-operational items needed to make sure everything is always up to standard.
For personal use, Costa created a batch conversion form. So say they need to supply 100 cases of product in a particular week. Costa simply plugs that amount into his form and it calculates the number of batches needed to hit their target. “It helps me plan my week quickly,” said Costa. “Nobody is going to make my job easier but me. So Device Magic has certainly helped in that aspect.”
Keeping Operations Lean with Device Magic
FGP Manufacturing is a lean operation tasked with supplying accounts of all sizes. Each team member wears many hats to contribute to the company’s overall success. Adding daily paperwork processing to the mix would have ultimately impacted their bottom line. This concern was eliminated when they partnered with Device Magic. And FGP looks forward to finding more and more ways to integrate the application into everyday operations.